The value in veneer
Merriam-Webster defines veneer as “a layer of wood of superior value or excellent grain to be glued to an inferior wood,” or “any of the thin layers bonded together to…
Merriam-Webster defines veneer as “a layer of wood of superior value or excellent grain to be glued to an inferior wood,” or “any of the thin layers bonded together to form plywood.”
That’s a pretty limited description because it implies that the primary reason for going with veneer is simple economics. In fact, a shop is more likely to choose this process over solid wood for a number of other reasons. These range from aesthetics to engineering. Veneer offers a woodshop the chance to arrange patterns as in book-matching or creating diamonds, squares and other configurations. It allows a designer to play with color and grain, mixing several species for dramatic effect. Veneering also conserves rare or threatened species, using about 5 percent of the material to deliver the same effects as solid 4/4 boards. Veneer can be used to build bentwood structures that curve in one graceful arc without any joints showing. It can twist and turn and be laid on intricate forms that are simply beyond the range of solid boards.
And, of course, MDF core is a lot less expensive than solid exotic wood cores when building large projects.
For shops that are thinking about ramping up their use of veneer, there are several aspects of the process to ponder. These begin with cuts, species and availability, but a good deal of thought also needs to be given to choosing the right cores, adhesives and clamping processes.
Choosing cuts
Veneers can be harvested from four main areas of a tree — the stump or root system, the trunk (bole) and from burls and crotches. Some burls are quite massive and can deliver very dramatic grain patterns, but that erratic growth can also present a lot of problems in the shop. It can be impossible to plane and sometimes it can be very difficult to clamp without breaking or cracking. Crotch veneers are about as dramatic in aspect, but are generally better behaved.
Mills harvest various grades of veneer, from commercial rotary cut red oak, maple and birch ply that one sees in the big-box stores to architectural grades that are often laid up (glued to a substrate) at the mill. Buying product that is already assembled has two sides to it: the woodshop doesn’t have to worry about glue and vacuum presses, but it also has to accept the available cores that the mill offers. If the work is just going to be flat panels, that’s fine. But a curved reception desk will probably need to be laid up in-house.
The most common cut is rotary. This is where the log is suspended between two live centers (or on an axle) and turned on a giant lathe. A long knife slices the veneer into a huge sheet as the log turns, almost following the growth rings. The result is a broad pattern that can be difficult to match up in panels, so the joints show. Wide logs have a very broad pattern and, as the log is pared away, the pattern closer to the pith (the center of the tree) changes and becomes tighter.
Some mills will split a log lengthwise and then turn each half log on a lathe to produce a slightly more manageable pattern.
Plain- or flat-sliced veneer is harvested when the log is stationary (not rotating) and a knife slides back and forth across it. The result is a stacked “book,” which is made up of individual pages or “leaves.” These are stacked in the same order they’re cut and the collective entity is known as a flitch. The biggest advantage here is that each leaf has a pattern of grain along its edges that matches up well with the next leaf. So a large panel might have a series of relatively uniform grain patterns that go from tight quartersawn to wide cathedral and back again.
Some species, principally white oak, lend themselves to quarter sawing more than others. The appearance is a tight, straight grain with medullary rays (flake) running across it. The log is first quartered and then each of the four segments is flat-sliced. The widest leaf will only be a little less than half the diameter of the log, but the grain pattern makes it very easy to match leaves and create much wider panels. Some logs might have deterioration in the pith and the cells surrounding it (that is, hollow logs) and these can often be salvaged by quarter sawing.
A few mills will offer rift-cut veneer and this is essentially quarter sawing done on a bias (at about 15 degrees). This reduces the amount of flake in white oak and delivers a grain pattern with very straight, tight lines.
Matched panels
The three main ways that leaves are arranged in a panel are book, slip and swing matches. A book match takes two leaves and opens them up like the pages in a book. The “hinged” edges are then joined. This means that the grain pattern begins along the centerline of the panel and two mirror images are revealed as the grain travels toward the outside edge. And, of course, the outer edges visually match up with the outer edges of the next pair of leaves, so the pattern can be extended across a wide board (the width depends on the diameter of the log and the flitch that it yielded). This is by far the most common way to create a pattern.
A slip match is easy to imagine if one thinks of a deck of cards. The dealer slides the cards to one side, fanning them so the top card travels farthest and the bottom one stays where it is. Unlike book matching, every other leaf isn’t turned over, so there is no grain match along the joints.
A swing match is the same as either a book or slip match, except that every second leaf is then turned end-for-end. This makes it less obvious that there is a pattern.
Book or slip matched pairs can be organized so that they cover a wide panel. Laying the pairs side-by-side is called a running match. When the pattern has to accommodate restrictions (for example, on a 36”-wide interior door), the leaves at the edges can be trimmed to the same width. This is called a balanced match. If there are an equal number of leaves in the panel, then a splice will end up at the center of the door (center match). If there are an uneven number of leaves, then there will be a full leaf in the middle.
Because they are so thin and the grain is therefore the same front and back, veneers can be used to create an endless number of patterns such as parquet, starbursts, diamonds, herringbones and so on. Whereas running matches can be used to cover the walls of an entire room, these patterns are usually reserved for smaller projects such as cabinet doors and box lids.
Balance and dye
There is a theory in veneering called balance. This calls for a second sheet of veneer to be applied to the back of a panel to balance the one on the appearance, or visible, face. People have been doing this for centuries and it makes sense in two ways. First off, think about the gluing operation. One spreads a liquid on one face of the core, but not the other. Most of the glues we use have a lot of water in them. So, getting one face wet can cause the core to change shape. It only makes sense to do the same thing to the other face to keep things balanced. The second sheet can be a lower grade: this “backer” just needs to be about the same thickness.
Secondly, most of the furniture we build is subject to decades of seasonal variations in humidity. And we tend to apply more coats of finish on the appearance face and maintain that face with other substances such as waxes and oils. Over time, that balance layer on the back might just help control the flow of moisture through that face and keep it somewhat in balance with the protected best face.
Because veneer is so thin (an average range is from 1/40” to 1/28”), it can be dyed with great success. The liquid will color all the fibers all the way through. Numerous companies sell pre-dyed veneer sheets and several offer multi-ply that has been manufactured with dyed sheets. The latter, when cut, reveals an edge with a rainbow of color and this is often used to dramatic effect, especially by wood turners. It offers some creative options for furniture builders, too: for example, it makes interesting wooden handles and pulls.
Cores
Veneer has been around a lot longer than MDF or plywood — examples go back 4,000 years in Egypt. But it really came into its own around the time of the Restoration (the reign of Charles II) in the wake of the austere rule of Oliver Cromwell. English furniture blossomed in the late 17th century and inlay evolved into a major commercial art form. This was also the time when Louis XIV built the palace at Versailles. All over Europe, exotic and decorative veneers were being laid up on solid wood cores to create decorative panels. Marquetry, incidentally, is the freeform version of using veneer to create artistic panels, while parquetry uses geometrical shapes.
An impressive number of these veneered wonders have survived as museum artifacts and many more are still in daily use in both public and private spaces across Europe. It’s not unusual for a middle-class British family to have a 17th century cabinet in the living room, highly inlaid with rosewoods, mahoganies and native species such as apple and walnut. So it’s difficult to accept the commonly held belief that solid wood is not a suitable substrate for veneer. It is perhaps more accurate to say that we now have better options.
If a shop chooses to use a solid wood core, it should be kiln-dried and of a species that shows little lateral (radial, across the grain) movement. Northern white cedar, for example, will move radially about half as much as white oak. Slow-growing species (with tight growth rings) tend to be more stable. In most species, sapwood will move more than heartwood. Quartersawn and rift cuts are far better than plain sawn lumber. Edge-gluing thin strips together will definitely be more stable than using a single, wide board, but not because the amalgamation shrinks or expands more. Rather, it is because ripping and regluing eliminates a lot of memory and stresses will now work against each other to minimize warping, cupping, twisting and other anomalies.
MDF (and MDO) makes a respectable substrate for most veneering applications, but it’s heavy and not always amenable to mechanical fasteners (for example, draw-slide screws can strip easily). It also has an affinity for gravity: if not properly supported, a wide horizontal panel will bow, so it doesn’t always make the best tabletops. In a vertical installation, it is quite stable and there are no pockets or voids. Because of its slightly polished surface, some experts recommend sanding MDF with medium-coarse grit to ensure the adhesive will have enough grip.
Standard veneer core plywood doesn’t always make a great substrate, but multi-ply such as Baltic Birch or ApplePly does. Because it is virtually void free and constructed from hardwoods, ApplePly machines like solid wood. In general, the thinner and more numerous the laminations (veneer layers inside the board), the more stable the end product will be. Veneer core plywood is made up of an uneven number of laminations with the grain cross-bonded in alternating layers. This adds a great deal of dimensional stability as no single layer has enough volume to impose its will on its neighbors. Multi-ply can be manufactured in a one-step operation, but a better alternative is the two-step process that builds a thick core, which is then sanded before the two final outer layers are added. Many plywood sheets imported in recent years have lost their outer veneers because of oversanding or failed glue, so it might be a good idea to go with a name brand from a reliable supplier.
Particleboard is less dense than MDF and the particles are not as fine. Hence, the surface can be a bit rough. And Masonite was not designed to carry a veneer.
Glues
For centuries, the only choice was hide glue. Today, there are adhesives that are specifically blended for veneer work and they perform well. Some are colored, so that seams don’t show. Others are made specifically for applying paper-backed veneer with heat (iron-on).
Before settling on an adhesive, think about your project and estimate how much “open” time you’ll need to work before the glue begins to set. You might also want to find out what the cure time is and the clamp time. These will determine how long the clamping device (vacuum bag, clamps and cauls) needs to be engaged and how soon the veneered parts can be machined.
If a shop is planning on using contact cement, check with the manufacturer before applying it to large sheets. There might be substrate recommendations, cure time guidelines, clamping suggestions, coating thickness and other parameters such as paper backing — all of which need to be discussed first. As always with new processes, test it on a small scale before committing to a larger glue-up. While it’s usually more fun to ask for forgiveness than permission, contact cement is unforgiving. One issue for woodworkers new to the process is that the coating they apply can be uneven and “bunching” or excess cement can eventually telegraph through a thin veneer. Another issue is cold creep: check with your supplier and describe the nature of the substrate. Also mention the finish being applied and ask if it will affect the cement.
Self-adhesive veneers (that is, sheets with a peel and stick adhesive) can work well for small jobs and repairs. Some of them tend to be a bit thick, so seams, especially on corners, can become visible. Again, test the product before committing to it.
Yellow and white glues are probably not the best choices for gluing veneer. Some variations of them have some creep issues. Again, the equation depends on the species, cut and thickness of the veneer and the nature of the substrate. The best advice is perhaps to spend a little money and buy a veneer-specific alternative.
Many pros suggest using urea-based plastic powder resin, which is essentially glue with the water missing. It dries hard and is the adhesive used in many plywood products. However, it’s essential that the entire surface is evenly clamped and the pressure remains in place for several hours.
PVAs can react over time to their environment (heat from direct sunlight or high humidity), just enough to cause problems. And some woodworkers claim that pre-cat PVA can have an adverse effect when used with some veneer species, especially maple (cracks and blisters). Check with the specific manufacturer or supplier to see if they can confirm whether they have had a problem with that.
Hide glue is perhaps best reserved for purists on small projects. Before choosing to go down that road, do an online search for “veneer hammering” and get familiar with the process. It can be a lot of fun with very rewarding results, but it requires some knowledge and experience before one might be comfortable offering it as a service to clients.
There are a lot of companies offering excellent vacuum systems for clamping veneer. To start researching your options, search for “vacuum press” in the Woodshop News Resource Guide at www.woodshopnews.com.
This article originally appeared in the April 2016 issue.
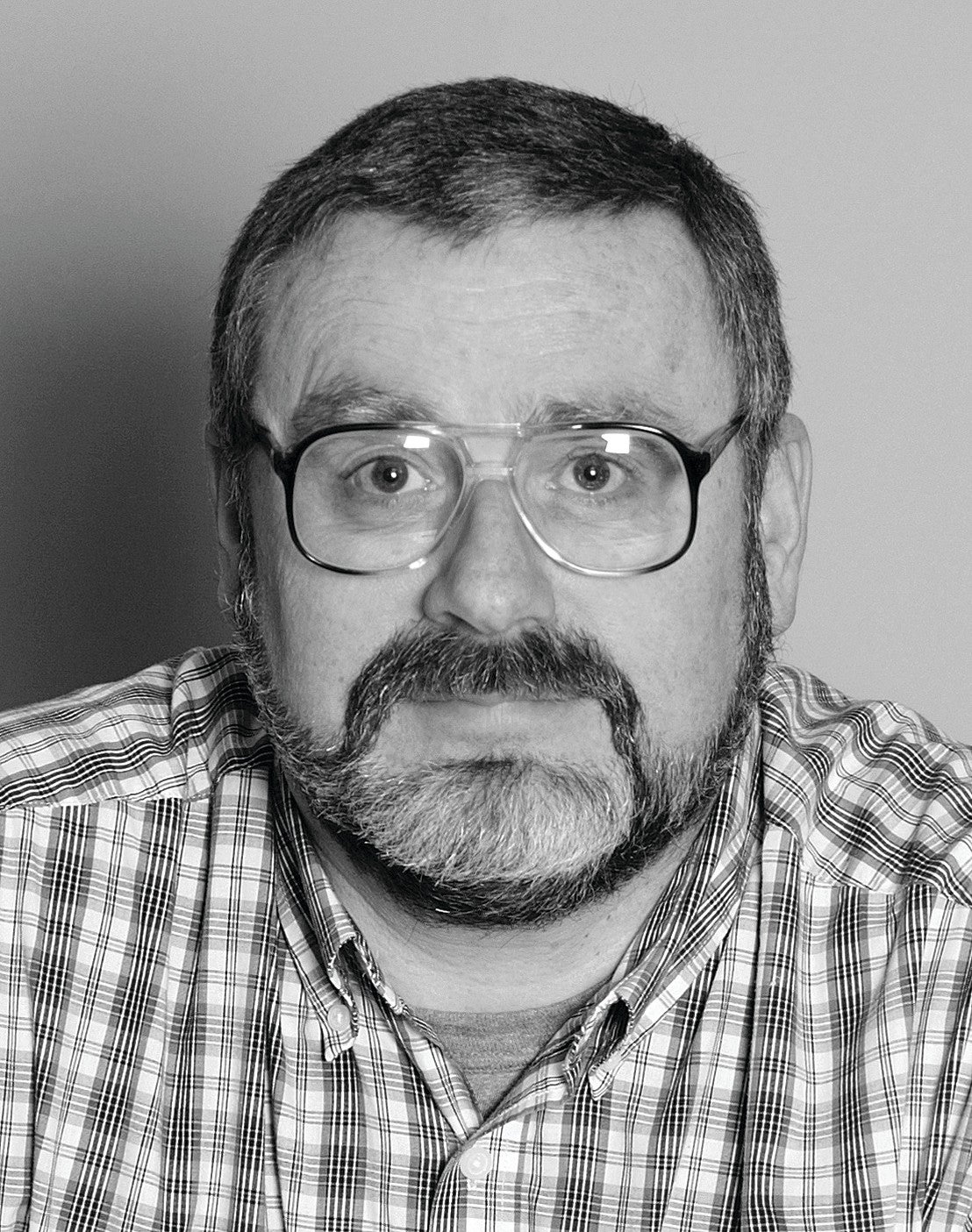