The view from 30,000 feet
It was a different year for the global woodworking industry in 2016. Both boom and gloom showed up in almost every market sector. While the economic recovery continues, it is…
It was a different year for the global woodworking industry in 2016. Both boom and gloom showed up in almost every market sector.
While the economic recovery continues, it is uneven at best. Sales are good, but costs are rising. Challenges have emerged during the last few years from disparate and unpredictable sources. Woodshop owners have had to deal with issues as diverse as health care reform, volatile organic compound (VOC) emissions, advancing technology, labor shortages, foreign competition and even the recent uncertainty in national politics, which is going to affect everything from minimum wage to international trade agreements.
Overall, though, the future for the domestic industry, at least during the next few years, looks quite promising. Let’s begin by taking a quick look at general economic trends in the U.S. and work down to some wood industry specifics.
One good indicator for the woodshop industry is the manufacture and sale of durable goods. These are defined as items such as appliances and furniture that continue to serve the consumer over several years, rather than being completely consumed in a short time. On Oct. 27, the U.S. Department of Commerce released its report on durable goods in the manufacturing sector and the August 2016 numbers for new orders edged down a hair (0.1 percent) while actual deliveries increased a healthy 0.8 percent. However, if one takes defense spending out of the equation, durable goods orders were up 0.7 percent.
That would seem to indicate a rather healthy outlook.
But in the tradition of boom and gloom, the government also reported that quarterly after-tax profits for U.S. manufacturing corporations are significantly down from their high in 2014 and indeed have shown a steady, though un-dramatic, decrease since then (about 13 percent). On the other hand, much of that can be traced to companies investing pre-tax profits in new machinery and equipment. And if AWFS and IWF numbers are any indication, that is certainly true for the wood industry.
At the retail level, furniture and home furnishing sales are up 3.8 percent during the last nine months and building materials are up 6.7 percent. Those compare well to overall retail sales, which are up only 2.9 percent.
Skilled labor shortage
In North America, hardwood and sheet stock performance is inexorably tied to the health of the housing and commercial construction markets. On Oct. 19, the Department of Housing and Urban Development reported that September’s building permits were up 6.3 percent over August and 8.5 percent over the same month last year. The numbers for buildings with five units or more were significantly stronger than single-family homes.
And here’s that boom-and-gloom aspect again: actual housing starts for privately-owned housing were down 9 percent in the same period (August to September 2016) and were 11.9 percent lower than in 2015. Housing completions were also down: 8.4 percent from August and 5.8 percent from a year ago. However, total construction spending (in all segments — residential and commercial) was only off by 0.2 percent in September from a year ago. So, units were down, but dollars weren’t. That would indicate a significant increase in unit cost.
There are several codicils here. The most apparent is that some regional markets have slowed down because of shortages in both materials and available labor. There has been a distinct tightening of both skilled and unskilled labor pools as unemployment numbers have continued to shrink. The recession also refocused large segments of the economy so that workers who had been trained in construction were forced to gain new and often unrelated skills and education as a means of surviving shrinkage in this specific industry.
Technology also has a lot to do with changes in the labor pool. Attendees at IWF in Atlanta were treated to a number of exhibits where robotics have taken over traditional roles and the woodshop of the near future is going to look a whole lot different than it does today. Skilled labor is taking on a new identity, where workers are becoming more adept at running robots than saws.
The U.S. isn’t alone when it comes to a skills crisis. On Oct. 31, Lloyds Bank in London reported that one-third of British contractors are facing significant challenges hiring skilled bricklayers, electricians, plumbers and joiners. The report, published in Builders’ Merchants News, also went down that gloom-and-boom path as it quoted Lloyd’s Pete Flockhart as saying: “Given the challenges that house builders face, the sector is painting a relatively optimistic picture, with improved growth and investment forecasts compared with last year’s survey.”
So, while labor shortages are hurting, demand for new construction is still strong for now.
That lack of skilled labor means that U.S. builders will be paying more in wages, and that increase in cost must be passed along to buyers. The net effect is that a construction boom has caused a tightening of material supplies and a shortage of skilled labor, which in turn is raising home prices, which seems to be having a negative affect on new construction starts. Whether these are simple growing pains or the beginning of a long-term trend is debatable at this point.
But the need to attract, train and retain skilled woodworkers and related trades is not debatable and indeed is becoming critical. On Oct. 30, Dan Nielsen of the Record-Eagle in Traverse City, Mich., covered some commentary from Home Builders Institute president and CEO John Courson. Courson told the paper that solving the shortage of skilled building trades workers is one of the most significant keys to keeping the U.S. recovery on track. “Housing historically has always been a driver of GDP. Every recovery we’ve had has been fueled by housing,” Courson said in the report. “Attracting young people to the building trades and training them has never been more important. The recession a decade ago slowed construction activity and left many construction workers idle. About 1.7 million skilled workers abandoned the industry. Most have decided to stick with the new careers they found after leaving the trades.”
Fortunately, those new careers may be just what the doctor ordered. When it comes to potential new employees, the woodshop of the future will be more in line with the skill sets of young people who know more about touchscreens than saw blades.
Competition for materials
A shortage of skilled workers isn’t the only challenge facing woodshops. According to the Hardwood Review (hardwoodreview.com), “global lumber demand in 2016 has proven stronger than every economic indicator that suggested, including the strong dollar, global economic malaise, and the hangover buyers should’ve had after the fall 2015 buying spree.”
High global demand for softwoods affects the availability of core fiber for sheet stock in the U.S., and strong demand for hardwood boosts door stile, face frame and other component costs. And if a local woodshop thinks global trends have little to do with its bottom line, it might be time to think again. Much of the current peak in demand is being generated in Asia. In November, Fortune (fortune.com) reported a significant bolstering in the services sector of the Chinese economy and the editorial concluded “the world’s second-largest economy is on a steadier footing. Beijing is increasingly counting on the services sector to create jobs and drive growth as it looks to shift its economic model more toward consumption from a traditional reliance on investment and exports.”
That fundamental shift in direction indicates maturity in the Chinese economy that will lead to more sophisticated and extensive commercial and residential construction and thus higher demand for wood industry materials. This, combined with a willingness in that economy to increase the use of credit, leaves some economists with the impression that interest rates could soon rise.
The trend from industrial to service growth in both China and several other Asian countries is fueling a need for new commercial construction to cope with an emerging middle class and its demands. That ties in with a Hardwood Review report that shipments of North American lumber this “year-to-date were up 19 percent to Asia and 10 percent to Europe.” One smaller facet to that is the fact that Asian paper mills are making serious inroads into what was traditionally a U.S. industry. Book, magazine and catalog publishers have increasingly turned to China for cost savings and the volume of paper pulp being used has had an impact on American wood markets. Some pulp producers in the Northeast have tried to switch to biomass energy as a replacement market, but that route is heavily impeded by environmental regulation.
The note about an increase in European demand also makes sense. Many European woodshops manufacture parts and completed product for Asian markets. For example, Turkey has a vibrant woodshop industry and indeed had a very strong presence in the most recent Las Vegas and Atlanta woodworking shows. If the trend continues — and there is no indication that it won’t — North American woodshops will face a gradual rise in both prices and demand for materials in the foreseeable future as other countries compete for limited resources.
Domestic lumber production in the U.S. might meet some of that demand, but strictures on imports, especially from Canada, will probably offset any gains. On Oct. 24, Wood Markets Group (woodmarkets.com) ran an editorial about the expiration of the U.S.-Canada Softwood Lumber Agreement. The group’s forecast seems to be that tariffs or quotas will soon be used to curtail imports and boost domestic prices. Canada currently supplies almost one-third of U.S. needs, which represents a significant amount of the raw material that is used to manufacture panels and other materials for woodshops.
Much of the lumber produced in the Eastern U.S. is destined for domestic markets. In the West, exports to China, South Korea, Japan and other Asian markets are more significant. The term “Midwestern” has traditionally referred to America’s heartland, but now it is being applied more and more to China. As that country’s midwestern cities continue to develop and grow, some of their supply chain for lumber is beginning to switch from Russia to the U.S.
There is a finite amount of commercially harvestable wood in the world and vast new Asian markets are beginning to emerge. If one relates that to a strong domestic housing market and the Federal Reserve “leaving the door open” to imminent interest rate increases, then long-term trends for higher wood prices seem preordained.
Industry trends
The world is changing and woodworking must change with it. While the great industries used to be basic, such as steel and railroads, today the largest profit centers are in high-tech fields such as pharmaceuticals and medical research. And though woodshops will always build residential casework and furniture, the nature of commercial projects is evolving in response to that. Shops are now building more clean rooms, research facilities, medical centers and laboratories. Part of the transition is an international awareness about the need to handle biohazards more intelligently to protect consumers and employees, but most of it is simply profit-driven.
Add to that the fact that the spaces we occupy are gradually moving away from organic products such as veneers and solid-wood panels and replacing them with more “sanitary” solutions. Americans who travel in Europe and the Far East can’t fail to notice the accelerating trend toward glass, metal and plastic in both design and architecture. Some of that is due to locally available materials or maturing tastes, but there is also a troubling medical undercurrent. As antibiotics become less effective and global travel increases, the planet’s population continues to rise (we just passed 7.4 billion). Many designers are predicting the emergence of what they’re calling the wipe-down world. It began with grocery stores offering antiseptic wipes for cart handles and people in some Asian countries wearing filtering masks on the streets. For woodshops, the trend means that more and more jobs will spec plastic and other non-porous, non-fibrous materials.
Robotics continues to make significant advances in the world of CNC milling and materials handling. While those physical changes are still in relative infancy, a look at automobile manufacturing facilities presents a chilling picture of the woodshop of the future: rows of robotic arms replacing those of woodworkers. It will be a little while yet before small- and medium-sized shops can take full advantage of automation as costs decline and machines become more accessible. But it won’t be too long before most of the workers on the shop floor are monitoring machines rather than running them.
Another and much more fundamental change is also working its way through the industry. Larger woodshops are becoming outsourcing suppliers and smaller shops are evolving into a more retail-oriented role, rather than a custom manufacturing one. The number of big shops that build components such as doors and drawers and wholesale them to other shops has increased dramatically during the last few years. And it’s no longer just doors: RTA (ready to assemble) cabinetry now represents a significant share of the market and many small shops spend more time selling and placing parts orders than they do running their own machinery. Consequently, much of what was once custom is now available as components and small shops are specializing in installations, sales and an occasional artistic manufacturing project.
This isn’t a surprise: the trend in most maturing industries is that supply gradually becomes centralized. One only has to take note of the number of large corporate mergers of late to see the pattern. The result, for woodworkers, is that small custom shops are beginning to occupy a niche, rather than remaining mainstream. Whether that will evolve the way the coffee shop fad has done or whether it devolves as outsourcing suppliers enter the big-box retail market remains to be seen. The industry will always need installers, but soon it might not need so many builders.
This article originally appeared in the December 2016 issue.
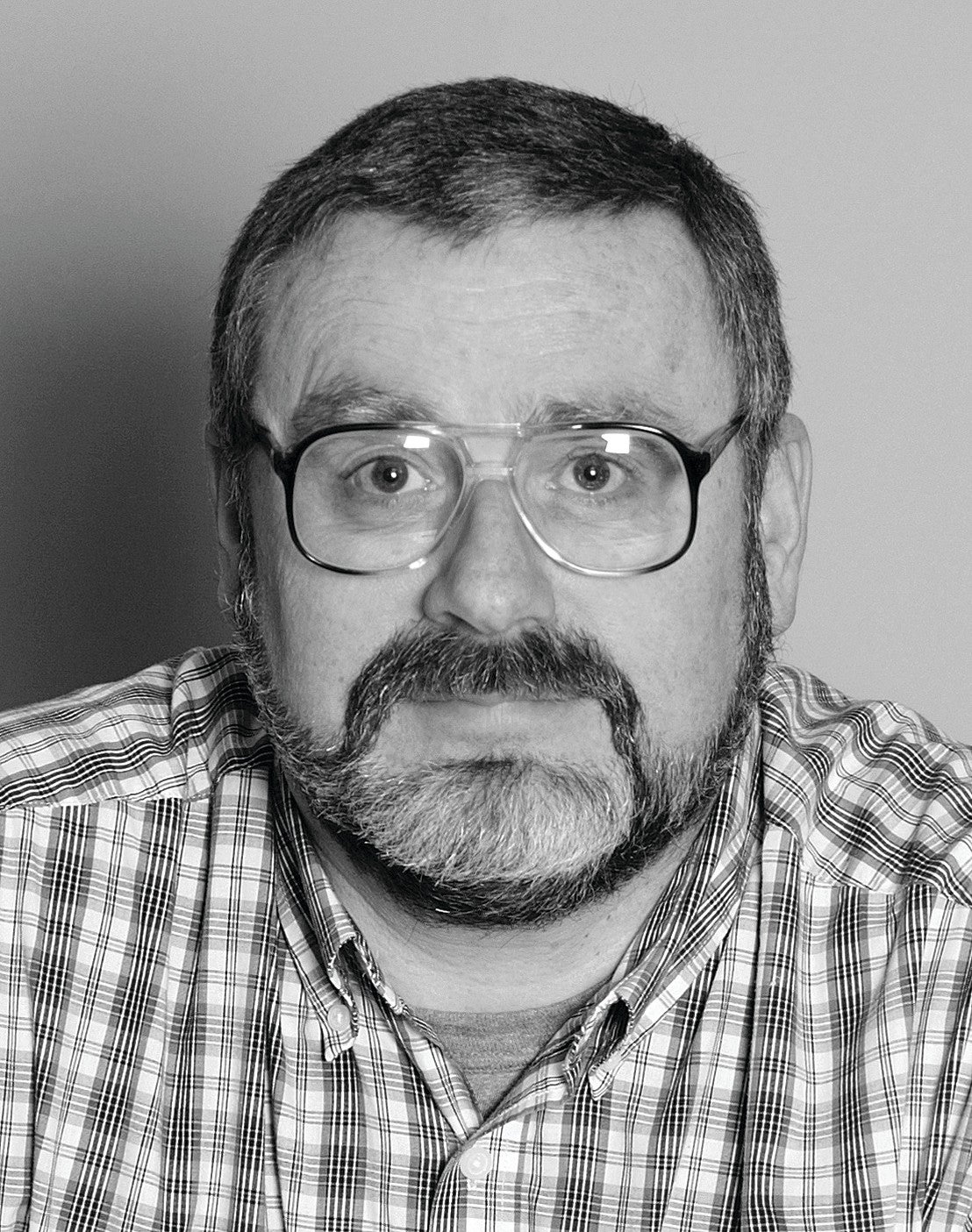