Three cheers for veneer
A woodworker’s guide to cuts, adhesives, substrates and more
Veneer can be purchased as a sheet (with or without adhesive applied), or as a pre-made, coated or raw panel with a substrate such as MDF or plywood, or as an edge banding tape, again with or without adhesive. Some jobs require all three.
There’s no such thing as a standard thickness for veneer. Mills adjust this dimension to accommodate variables such as the rarity of the species, grain direction, cut, and density of the wood. Large commercial customers often require specific thicknesses. For example, some Japanese furniture manufacturers ask for extremely thin cuts from its most valuable logs, while chains offering knock-down, DIY furniture may use thicker cuts of less expensive species. There are some norms when it comes to thickness, and those have been getting a little thinner as technology makes it easier to do. Many mills now supply straight-grained, well-behaved hardwoods in a range of thicknesses from around half a millimeter (that’s 0.02” or 1/50”) to 2-1/2 mm (a hair over 3/32”). Perhaps the most common spec for commercial veneer is a thickness in the vicinity of 1/42” (0.0238”).
Veneer allows woodworkers to create large objects with unbroken grain patterns, such as a wall of doors and panels. This can be visually stunning, especially on a large scale. Veneer also helps avoid the unpredictability and movement associated with edge-glued solid boards, as an MDF or plywood core is far less likely to react to seasonal changes in the environment. And veneering can save money if a rare or expensive species is sliced thin and spread wide.
There are basically two ways to create veneer. A rotary cut is the least expensive and involves suspending a log between centers as one would a spindle blank on a wood lathe, and then rotating it into a knife. The second method is to use a knife to slice across the log while the wood is stationary. The rotary cut delivers a wide sheet of veneer with a broad pattern in most species. It’s often found on the back of a sheet where the front is an appearance grade high value species, or as the good face on sheet stock found in big box retail stores, or as a paint grade.
Sliced veneer can be quartered (as in having the look of quartersawn solid stock), rift or plain sliced. Quarter slicing gives the woodworker tight, straight, thin lines, which means edge matching can be a little easier. It features decorative medullary rays (flake) in some species. Rift slices are cut at 15 to 30 degrees and that eliminates most of the medullary rays but still delivers a straight, tight pattern. This is one of the more expensive cuts because there’s so much waste and a lot of setup and milling time.
Plain slicing is the most common cut, and it results in a familiar cathedral grain pattern that shows up a lot on hollow core doors and more affordable kitchen cabinets.
Some veneers are intentionally sliced to reveal drama, such as burls and crotches. Burls are growths that occur on the side of a tree trunk or down near the base, while crotches are harvested where the main trunk branches off to form a Y.
The most defining aspect of working with veneer is perhaps scale. Large shops use veneer as sheet stock in casework or perhaps to laminate entry door skins, while small custom shops might only make a few cabinet doors every year or even just do a few small repairs or cover a curve or two. In most cases, glues and substrates on sheet stock are determined by the mill or are specified by an architect and applied at the mill. For smaller projects, those decisions are left up to the woodworker. And for intermediate scale projects, veneer presses come into play.
Veneer adhesives
The thing to keep in mind when gluing veneer is that it’s very thin, so whatever happens to the substrate is probably going to telegraph through the veneer. There are a lot of discussions about whether to use hide glue, aliphatic resins, contact cement or other solutions.
Franklin makes an adhesive called Titebond Cold Press (titebond.com), formulated for cold press laminating of wood veneer to solid woods, particleboard, MDF, plywood and other porous materials. The two big advantages over contact cement are that this non-flammable product doesn’t set too fast or too slow (there’s a 15-minute window for adjustment) and it doesn’t emit harmful fumes. It also prevents bleed-through on open-grained and unbacked wood veneers, which is a big advantage with figured grain. A mechanical spreader is recommended, and clean-up before curing is with a damp cloth.
Better Bond X-Press is a fast-setting veneer glue with an advanced fibrous-resin additive that reduces bleed-through issues in all wood veneers. Available through veneersupplies.com, it is specially tinted to reduce glue line visibility and fill voids in burl veneers. It works with most standard-thickness domestic and exotic wood species. From 45 to 60 minutes of clamping time is needed, and the company says that its reusable glue roller is the recommended tool for applying this adhesive. It’s formulated for vacuum press veneering but will also work with many other veneer clamping methods.
Veneer Supplies also stocks Ultra-CAT veneer glue, which is a high-solid content, pre-catalyzed powdered resin with an extra-long open time. It was developed using catalyzed adhesive technology and it cures rock-hard. That eliminates veneer creep caused by seasonal humidity changes, and it also prevents joint lines from separating. It will permanently lock in the form of curved and contoured veneer projects, and that makes it suitable for bent laminations such as curved doors, skateboards or guitars.
Bob Morgan at Veneer Factory Outlet says that the three most common ways to glue wood veneers down are a self-stick, 3M peel and stick adhesive, or two coats of contact cement on both surfaces, or using woodworker’s glue such as Titebond II and applying pressure with clamps. Bob has an interesting article at veneer-factory-outlet.com that should be quite interesting for shops doing occasional veneering or small projects.
Vacuum clamping
This is the preferred way to apply larger sheets of veneer and manufacturers offer some clever solutions.
For example, Vac-u-Clamp (vac-u-clamp.com) designs and builds commercial vacuum clamps for veneering in California and offers three ranges of presses. The company’s FP model is a folding press that can fold up to a vertical position and be pushed up against the wall for space savings in the shop. The SP (standard press) is available in 4’ × 8’ and 5’ × 10’ sizes and includes standard equipment such as oil-cooled rotary vane vacuum pumps and a silicon membrane. And the TP (table press) is made from the same aircraft aluminum as the SP and is designed to sit on the table the shop builds.
Vacuum Pressing Systems (vacupress.com) offers a full range of veneering and laminating products including flip-top table press kits, vacuum pressing bag systems, Vacupress vacuum pumps, veneer glue and specialty veneering tools.
Then there’s Quality Vakuum Products (qualityvak.com), which offers pumps, presses and a wide variety of veneering accessories such as cutters, glue spreaders, rollers, tapes, tubes and clamps.
Visit the Joe Woodworker site (joewoodworker.com) for tips and tricks on vacuum veneering.
Veneer substrates
Historically, the substrate of choice for veneer was a lesser wood with a stable nature, such as poplar or alder. The veneer was laid so that its grain matched the grain direction of the substrate, to avoid cross-grain bond failure. Solid wood substrates were best made from straight stock such as quartersawn or rift, which was a bit of a problem as these are the most expensive cuts. Softwoods were widely used, too. When plywood came along, its alternating laminations gave it both strength and stability. The thin veneers stacked one upon another at right angles didn’t allow for much cross-grain movement. But plywood can warp if stored incorrectly or exposed to the elements.
Next, even more stable composites such as MDF and particleboard became popular substrates because they had no grain, and therefore no movement of consequence in any one direction. It didn’t take long for woodworkers to figure out that most substrates benefitted from having a backer, and still do. This is a lesser grade of veneer that is applied to the hidden face of the substrate, to balance it and hopefully avoid warping. It’s a good idea to finish this face as well, as the coating will allow both faces to absorb or release moisture at essentially the same rate and thus avoid any imbalance.
The two keys here with these materials are that they were much less expensive than the veneer, and they could also be rendered flat and remain essentially so.
To be frank almost any flat, stable surface can be used as a substrate for veneer, so long as the adhesive sticks. It must, however, be dry. That is, the moisture content must be close to the relative humidity in the woodshop, so it’s a good idea to let substrates acclimate in the shop before using them. And each face should be flat but not microscopically smooth, as a minutely scuffed surface will adhere better than a polished one.
Veneer resources
Certainly Wood
Raw wood, full-length veneers
certainlywood.com
716-655-3446
DC Distributing
Edge banding and related products
dc-dist.com
800-727-0917
FormWood Inds.
Plywood, veneer sheets and edge banding
formwood.com
812-284-3676
Frank Paxton Lumber Co.
Echo Wood, reconstituted real wood veneer
paxtonwood.com
888-826-5580
Hardwoods Specialty Products
Veneers and substrates
hardwoods-inc.com
888-826-5528
Herzog Veneers Inc.
Domestic, exotic, dyed and recomposed veneers
herzogveneers.com
336-434-4053
KenCraft Co.
Veneers and panels
kencraftcompany.com
419-536-0333
L.L. Johnson Lumber Mfg. Co.
Veneered panels
theworkbench.com
800-292-5937
Lenderink Technologies
Veneers and panels
woodveneers.net
616-887-8257
Northwest Lumber Co.
Paperback 10 mil veneers, panels and edge tape
northwestlumberco.com
800-252-930
Oakwood Veneer
Veneer sheets, panels, banding
oakwoodveneer.com
248-720-0288
Parkerville Wood Products
Hardwood veneered plywood
parkervillewoodproducts.com
860-649-9663
REHAU Industries
Edging
rehau.com
703-777-5255
Rugby Architectural Building Products
Hardwood plywood, composite panels
rugbyabp.com
855-650-3265
Superior Veneer & Plywood
Manufacturer of Spicy Sheet veneer and plywood
superiorveneer.com
855-940-7827
Rockler Woodworking & Hardware
Small order veneer, edge banding, glue, clamps
rockler.com
800-279-4441
The Wood & Shop
Hardwood veneers
woodnshop.net
314-739-0001
Woodcraft
Small order veneer, edge banding, glue, clamps
woodcraft.com
800-225-1153
Woodworker's Supply
Small order veneer, edge banding, glue, clamps
woodworker.com
800-321-9841
This article was originally published in the August 2021 issue.
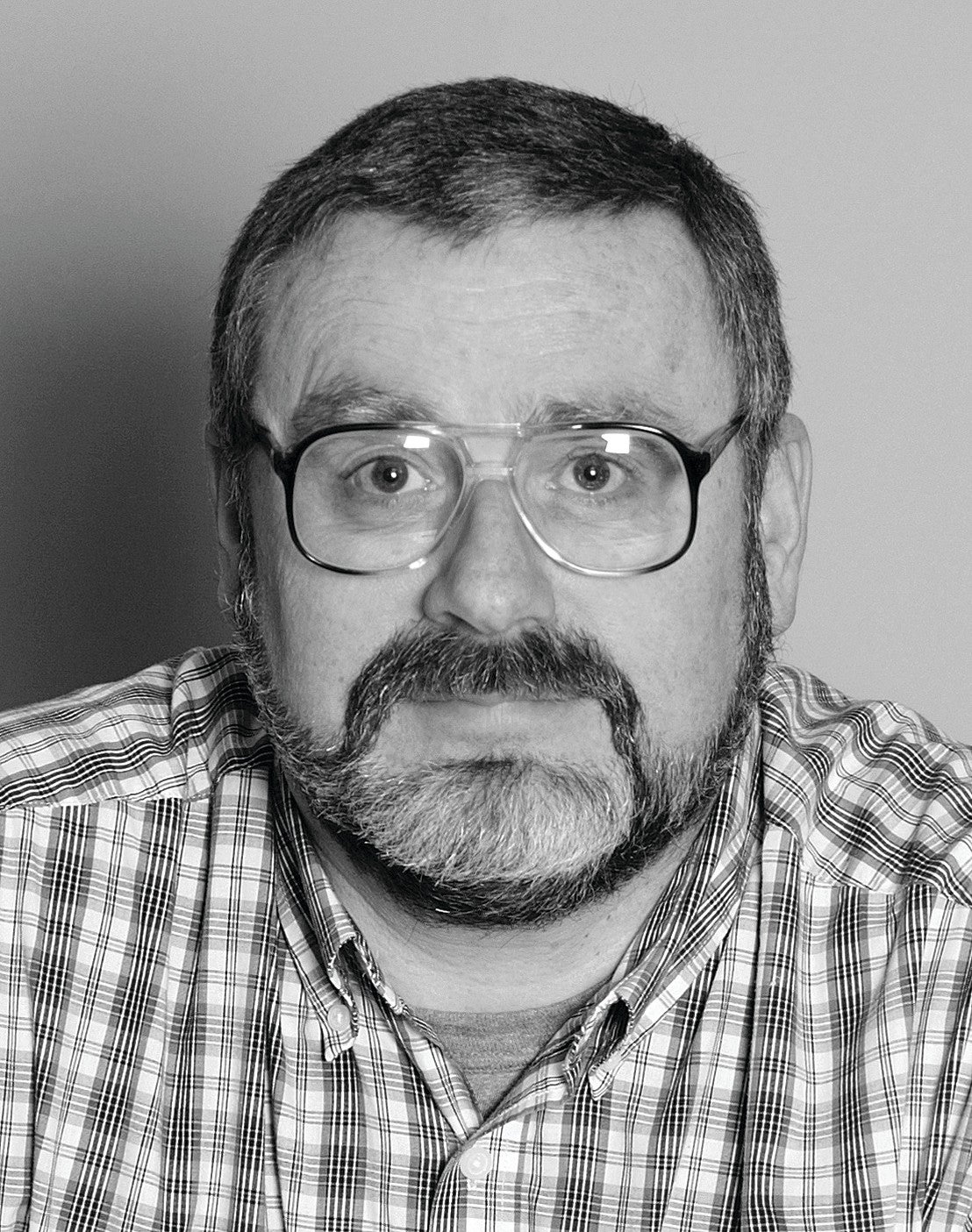