Tooling time
Finding and ordering CNC tooling is easy, but knowing what to order can be a bit trickier
What choices does a shop need to make when purchasing CNC tools?
Tooling requirements depend on parameters such as the material being cut, the length and depth of the cut, the number of cuts, the travel speed and rotation of the bit, the size and geometry of the flutes, the tool material, and even the toolholder. A good place to start is to become familiar with the concept of chip load. This measures the amount of material being removed by each flute or tooth of a CNC tool as it progresses through the job. Industrial manufacturers will provide an optimum chip load range for tools, while consumer router bits don’t usually come with that information. Staying within the recommended range will help control the torque stress (sideways force) being applied to the shank, collet, toolholder and spindle, plus the amount of heat build-up, the wear on the tool edge, and ultimately the quality of the part being made. Too high a chip load can even cause the machine to draw more amperage because of increased resistance. As a rule of thumb, wider bits will have higher chip load ratings, but that can depend on the profile.
Hardwoods, softwoods, MDF, plastic laminate or melamine can all behave a little differently when being milled or shaped. Sometimes a shop just needs to create edges that will slip into dadoes or grooves and never be seen again, so speed might be more important than the quality of the cut or edge. In that case, a simple one-flute bit might be all that’s required. Or a shop may have a CNC with limited horsepower that requires slower travel and shallower cuts, so up or down spiral bits may be the best way to remove waste and reduce stress. The workpiece might have a delicate laminate or veneer on its faces and the cutter needs to avoid tear-out. Some bits pull up, others push down as they exit the cut, and some shear-cut bits can do both.
There may be clamping parameters and methods that reduce or increase the amount of waste that can be removed in a single pass. Material density and hardness may play a role here.
The profile of the cut is a key element. There can be a big difference between, say, carving and engraving, and the bit size and cut speed may vary dramatically between the two. Think about this: the same machine can run an acute V-bit to scribe a pencil-thin signature or run a large and very wide spoil-board bit that’s being used to level a surface.
There may be physical restraints, too. The tooling needs to work in the woodshop’s available collets and toolholders, and in smaller CNC machines the shaft length can be an issue if there is very limited Z travel.
Deciding factors
There’s a trade-off between speed and torque in CNC tooling. Speed is a two-part concept. There’s the rate at which the spindle spins (measured in rpm), and the rate at which the bit is fed in X and Y under load. Tools are speed rated for rpm and larger tools obviously need to rotate at slower speeds. But narrow bits also have limitations, and they can heat up quickly and even snap if they’re asked to plow too deep or too fast. It’s a good idea to avoid settling on a narrow tool to remove a lot of waste when the shop doesn’t have a wider one on the shelf. A visit to the supplier or a day’s delay for overnight shipping on a larger bit might save time, because using the smaller bit will take longer and cause more stress on the bit, the machine, and possibly the operator.
So, choosing tools isn’t just about the tools – it’s about the work they will be asked to do, plus the speed at which that work will be done. And how well a tool meets those requirements is the best way to evaluate its cost. The sticker price on top-end tools can be daunting, but that’s not the true price. Think more in terms of the amount of material the tool can shape, cut, or remove over its entire life, rather than how much its cost eats into the profit on the single job or project for which it’s being purchased. In other words, how many linear feet of work will it complete between each sharpening, and how many overall feet before it needs to be replaced? In bookkeeping terms, tools are not just a cost of goods sold, but rather an investment in equipment.
There are hidden costs in buying inexpensive tools. There will be more rework, more burned edges to sand out, less accuracy, more chatter, poorer finishes, and more downtime spent changing out bits for sharpening or replacement. Parts take a little longer to make, and the extra few seconds or minutes over the course of a large job can add up to hours.
Unfortunately, price is just an indicator as to the quality of a tool, and not always a very precise one at that. For example, some PCD tools will outlast carbide by several factors, but they may not produce quite as crisp an edge. Diamond tools are usually HSS or solid carbide bodies with PCD grains on the cutting flutes or tips. The profile that a shop requires may be available in high-speed steel, solid carbide, carbide tips brazed to a steel shaft, replaceable carbide inserts, or diamond. Deciding which one to buy comes back to estimating how many linear feet it will be asked to cut over its useful life. If this is an unusual profile and a limited run, that’s a much different life than the one that will be enjoyed by a straight spiral bit that will be used repeatedly over time.
When it comes to complex profiles, one advantage to choosing insert tooling over solid bits is that inserts are more likely to be accurate when replaced. Solid bit geometry can change a little, especially if the supplier changes machinery, materials, or processes.
Ordering online
With a pretty good idea of what is needed, the next step is to find the website of a reputable supplier and then navigate the online menu. For example, the Wood Tooling Shop (woodtoolingshop.com) in Wilmington, N.C. has a typical shopping cart that lets a woodworker select router bits for nesting operations. After reaching the right page in the catalog, the woodworker will have several choices to make. A PCD shear bit will have a design that mixes various numbers of cutting surfaces for up-cut and down-cut contact with the work. For example, a 3+3 shear cut design is intended to deliver a clean finish on both the top and bottom surfaces of a workpiece with the same or similar outer laminations. Other combinations are more appropriate when the sheet material being routed has two different exterior laminations, so it’s important to discuss that with the sheet stock supplier before shopping for a tool. The Wood Tooling Shop site then offers choices for various bits in the cut diameter, cut length, OAL (the bit’s overall length), the shank length, shank diameter, the material used in the plunge point (carbide or diamond), the number of tips, and the type of body (steel, solid carbide).
Sometimes there just isn’t an over-the-counter solution and a shop needs to order a custom, one-off tool. Full-service shops such as Connecticut Saw & Tool, or specialty shops such as Active Tooling, ASAP, or Vortex can offer stock bits but also make custom profile knives, insert tooling, diamond tools or brazed cutters. Connecticut Saw & Tool uses in-house 5-axis CNCs to tailor-make insert tooling that has flawless profile repeatability, and the staff will discuss aspects such as varying carbide grades to match the material being cut. As with most custom manufacturers, the process begins when a woodshop emails a drawing, faxes a sketch or ships a wood sample to the tool supplier.
This article was originally published in the March 2022 issue.
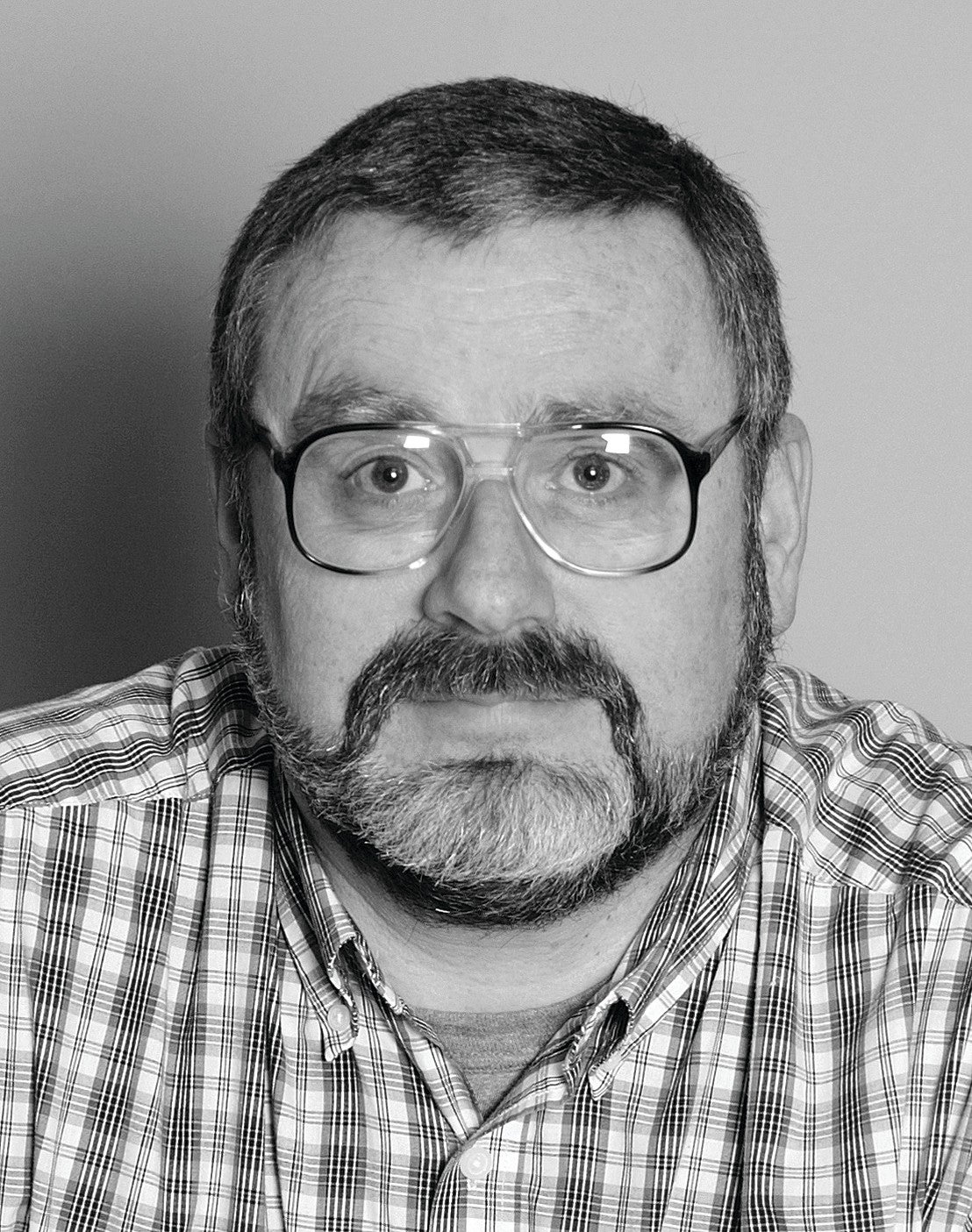