What’s in your glue?
The chemistry and characteristics of edge banding adhesives.
There are a lot of options when a shop starts to edge band, including selecting the right machine, glue and material. Knowing what’s available can help a woodworker get better results. For example, there’s more than one hot melt glue, and most of the available adhesives can be formulated in different ways to improve the bond between the tape and the substrate materials. The technical term one comes across most frequently here is polymer, and that’s a building block for plastics or resins which is made up of lots of similar molecules that are chemically bonded together. Another common term, copolymer, simply refers to a mix of two or more polymers that are combined to achieve a product with more bonding, curing or endurance characteristics.
Types of glue
Ethylene vinyl acetate (EVA) is a copolymer that is often called ‘EVA rubber’ but actually doesn’t contain any natural rubber. It’s a plastic foam that’s made from ethylene and vinyl acetate, a combination that delivers a very elastic product that becomes stronger but remains tack-free and flexible as it cools down to room temperature. It’s also resistant to UV radiation and cracking, so it’s a good choice for furniture that may be placed in sunlight. EVA products can be glued with contact cement, which helps with repairs.
EVA has been around a long time, and many shops are comfortable with it. They like that it has short open and set times. That is, it cures quickly. EVA can also be formulated to meet FDA guidelines for food contact. Ethylene is a hydrocarbon, which is an organic chemical compound that’s made up of only hydrogen and carbon atoms. It’s a colorless, flammable gas that smells slightly sweet, as does the other ingredient in EVA, vinyl acetate. This latter is a monomer (that’s just a molecule that bonds to other molecules like itself) that takes the form of a volatile, flammable liquid. So, EVA hot melt glue is essentially a gas and a liquid that are combined to make a glue that is stable at room temperature and becomes viscous (a thick and sticky liquid) at higher temperatures.
Polyurethane reactive adhesive (PUR) is the next most common option for edge banding. It’s a little thinner than EVA and accepts more coatings such as varnishes. Most application will require less PUR than they would EVA, which means there are fewer squeeze-out possibilities. PUR be a little more expensive in terms of both the product itself and machinery. It takes longer to cure, and PUR can also emit diphenylmethane diisocyanate. PUR is fast, and it delivers a very strong bond. It uses humidity in the air and moisture in the substrate to help it cure, and it won’t remelt, or forgive mistakes. It’s also topical: it stays on the surface of the material, rather than soaking into the pores, and that can leave a visible joint line. (Many hot-melt glues can be tinted or color-matched to blend with the tape or panel and produce a less visible line where edges meet.) Because PUR sets so quickly the edge banding process needs to be well-managed and continuous. Again, PUR sets fast, usually can’t be repositioned because of that short window, and continues to gain strength (known as cross-linking) as it cures because it is still absorbing moisture from the environment.
Another more expensive option, polyamide hot melt adhesive (PA) can be the best solution when the woodshop is bonding plastics that other hot melts don’t accept well. Some (not all) PAs can even create a strong bond to PVC, which is notoriously difficult to glue. They can handle a wide range of temperatures and they can be quite resistant oils, grease and other contaminants. PAs are used to fill holes, knots and cracks in substrates. Some of them can also resist mild acid and alkali solutions, which may make them more suitable in lab or clinic casework.
When working with PAs, the formula can often be ordered to provide a specific range of open times, from fast to slow, depending on aspects of the edge-banding process such as the size of the panels, width of tape and speed of assembly. Unfortunately, that flexibility means they usually have a short shelf life (check with the supplier). They also should be in a sealed tank because oxygen and humidity can affect their adhesion qualities. PAs are often greener choices than other hot melt adhesives because they’re made with organic ingredients rather than petrochemicals. That can also mean that they’re not as flammable, volatile or combustible as some other choices. They don’t have an odor, and they come in a variety of colors. Woodworkers are strongly advised to consult with a product expert before assuming that a particular PA will solve a specific challenge.
Polyolefin-based (PO) hot melt adhesives are also more expensive than EVA glues, and they can work a little better with plastics and lacquers. They remain more stable at higher temperatures and if they’re formulated for a long open time, they can be sprayed.
APAO (amorphous poly alpha olefin) hot melt glues are used in the auto, boat and RV industries and in applications near coastlines or other environments where corrosion and moisture are factors. They are particularly good at bonding plastic and metal, and at handling high temperatures.
Some glues are two-part, some come in sticks or cans and others are in pellets or cartridges, and some shops don’t even use hot-melt glue for edge banding. They prefer contact cement or even standard woodworking glues, depending on the application and materials to be bonded.
So, which glue should you use? There’s no simple answer. You’ll need to discuss it with your supplier and before you make that phone call be sure you know what the substrate is, what the panel coating or its exposed top laminates are, which edge banding you’ll be applying (vinyl, metal, wood etc.), and what the casework’s ultimate use and destination are such as home, hospital, lab, manufacturing environment and so on.
Types of edge banding
The tape material can be metal, plastic, acrylic, melamine or a species of hardwood veneer. Some machines don’t use tape: they extrude a thermoplastic that literally makes edging from liquid as the board edge passes through.
Polyvinyl chloride (PVC) is a thermoplastic resin that can be heated to change its shape, malleability and viscosity. The tape comes in a range of thicknesses and widths, and higher quality products have pigment or patterns that run all the way through (solid color). That’s a big consideration if the shop wants to create invisible or at least low visibility seams as solid colors can be lightly sanded to blend them. PVC bandings are generally impact resistant, easy to work, easy to match to vinyl and melamine panel colors and patterns, and they are generally available in a pre-glued option for hot air application. A rule of thumb is that the harsher the environment, the thicker the tape should be. For example, thin tape can be used to edge drawer sides while thicker stock is more appropriate for countertops, hardware-free doors and open shelves.
Acrylonitrile butadiene styrene (ABS) is another thermoplastic but it’s a less dense option than PVC, and it’s also a greener choice because it can be easily recycled. There is no chlorine, and no acid, so it doesn’t emit greenhouse gases when it is burned. The residue after cremation is biodegradable and non-toxic, and ABS can even be melted and recycled. It’s about as durable and serviceable as other plastics, and resists heat well so it can be used adjacent to stoves and ovens. It’s very flexible, so it works well on curves and some other profiles.
PP or polypropylene edge banding is a flexible thermoplastic that can be split rather easily along its length. Because of its green aspect, it has been gaining ground in the U.S.
Polymethyl methacrylate (PMMA, or acrylic) is a rigid, less flexible, almost glass-like option that is most often considered for straight edges.
Wood veneer tapes can generally be ordered with a stain and coating already applied, are easy to glue, work and bend, can deliver the appearance of a solid board and are a familiar material for woodworkers. Of course, to use them the shop needs to sell natural wood casework which is becoming a more difficult proposition as time goes by.
Types of machines
Different glues work with different machines, so a shop needs to sort through the adhesive choices before considering an edge-bander. The primary consideration when purchasing the machine is probably going to be scale. How much tape will the shop apply, and how wide does it need to be? What functions are standard and which are optional? A small shop that will only edge-band a few cabinet doors each year may only need an over-the-counter clothes iron. A woodshop building thousands of doors will need to explore speed, trimming and other options such as integrating the machine into a work cell and adding workstations and operators.
There are machines that simply heat the glue and squeeze the tape in place with rollers, and there are machines that will trim the ends, top and bottom of the tape, buff the corners, dispose of the waste and even apply different degrees of pressure across the face to produce a very slightly convex product.
This article was originally published in the May 2021 issue.
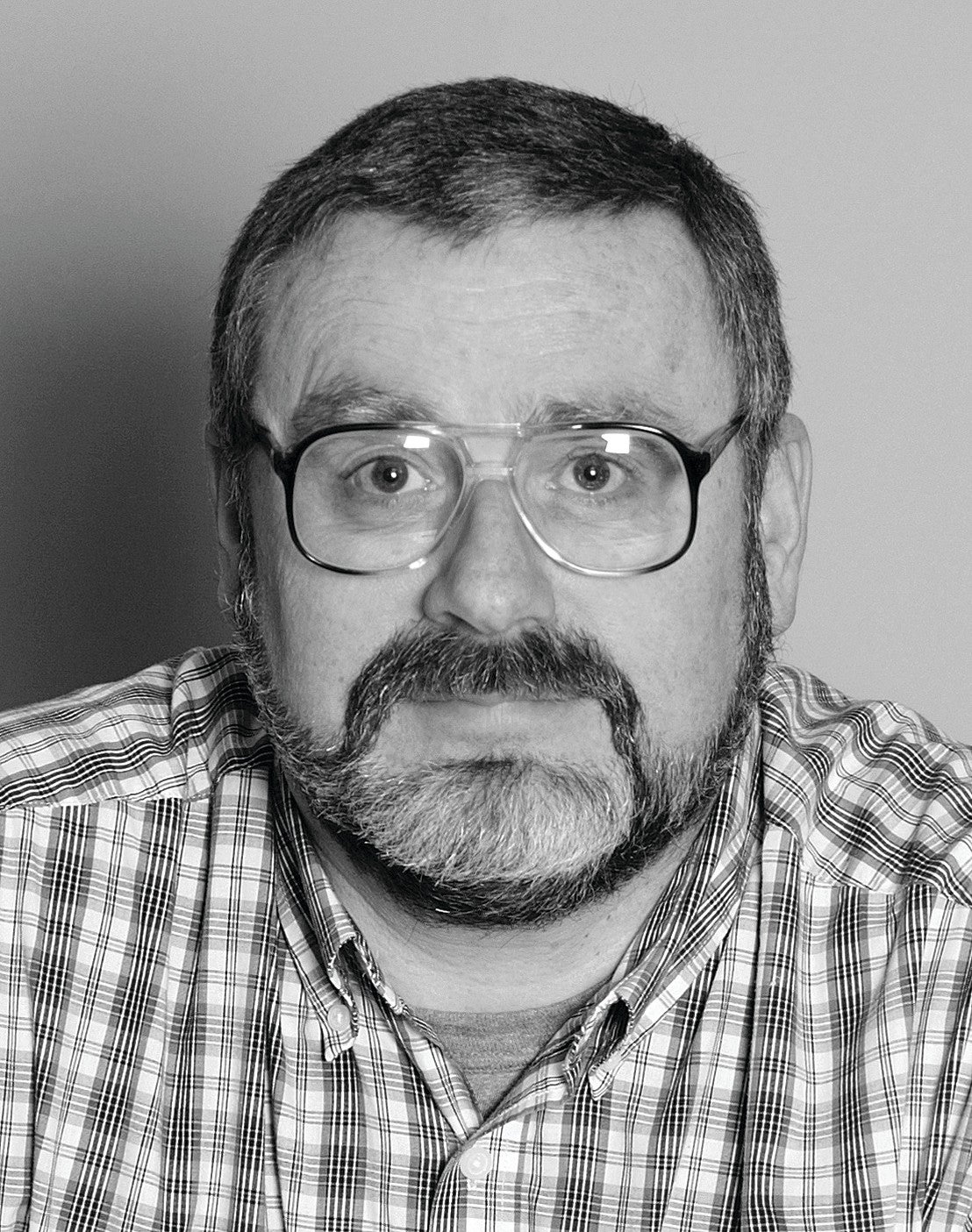