Where the rubber meets the road
A working spindle is essential for a CNC shop, while an aggregate head is an enticing option
As with almost every aspect of doing business nowadays, high-tech components and repair parts for CNC spindles and aggregate heads can be a challenge to find, especially for units that were made overseas. Even the most American-sounding manufacturers use parts from other countries, which they qualify in advertising by stating that the machine was assembled in the U.S. using globally manufactured parts. If a shop is using spindles made in Germany or China, odds are any replacements or parts are sitting in cargo containers outside a warehouse somewhere near the Suez Canal or maybe even in a New Jersey dockyard. As America experiences a construction boom and orders for custom cabinets and furniture back up, the good times can be derailed very quickly if a key component in the production cycle fails. For shops depending on a CNC (or several of them), one of the most vulnerable elements in the manufacturing process is the spindle.
CNC Parts Dept. (cncpd.com) supplies Hiteco, HSD, Perske, PDS and Giordano Colombo spindles to the U.S. market. The company notes that spindle motor lead time and availability are not exactly reliable with the current supply chain woes. While in-stock motors can ship within a day or two, out-of-stock lead times can be up to nine months or longer. So, the parts department is strongly recommending that woodshops keep spare CNC spindle motors on hand to avoid costly downtime.
That sentiment is echoed by the service team at PDS (spindlerepair.com), where the focus is on monitoring and servicing existing spindles. The company, which has rebuilt more than 40,000 spindles, now offers a Spindle Health Monitoring System that uses vibration and temperature analysis to help predict problems before they shut down production. The miniaturized system can be installed directly in new spindles or retrofitted to existing units, and it provides real-time monitoring that can reduce a machine’s downtime by predicting or detecting malfunctions. The sooner a shop knows there’s a problem, the sooner it can plan a way around it.
Because of the construction boom, many shops are working longer days and that means more hours on spindles and aggregate heads. One option for dealing with Covid-related supply woes is to look at remanufactured or refurbished spindles if new ones aren’t immediately available. Some of them actually exceed the original manufacturer’s specs and performance, and they usually come with excellent warranties. Last year, PDS introduced its PrecisionCare optional warranty program for new, repaired, and rebuilt spindles. It provides customers with a cost-effective warranty as well as post-sales service enhancements for PDS products for up to two years or 4,000 working hours, whichever occurs first, from the date of end user spindle installation. Other repair shops offer warranty programs too, so if a new spindle isn’t in stock, ask about a refurbished one. At worst, it will keep the shop humming while the original one is being worked on.
In these uncertain times, keeping spares on the shelf, keeping an eye on temperatures, and keeping rebuilt spindles under longer warranties all make a lot of sense. Avoiding a silent woodshop is all about vigilant maintenance. There’s a very interesting piece on the MultiCam website (multicam.com) about extending spindle life. Written by Lindsay Luminoso from Canadian MetalWorking magazine, it focuses on metal machines but most of the pointers offered are just as applicable to woodworking spindles.
Aggregate heads
Getting the most CNC for your money is more than maintenance and supply issues, especially for small- or medium-sized woodshops. That’s because budget concerns usually restrict how much machine a shop can justify, and there’s a big jump in the cost of a 5-axis machine compared to a 3-axis unit. Aggregate heads can help bridge that divide without breaking the bank, and they can help squeeze every advantage out of a 3-axis router. They allow the machine to complete more tasks, which means there’s less handling of sheet stock and parts. That speeds up production and helps avoid any bottlenecks caused by downtime for re-fixturing.
There’s a downside, too. Aggregate heads can heat up faster than a straight spindle, so they work best on short tasks rather than prolonged engagement. If an operation can possibly be completed by a standard spindle, save the aggregate for specialty work. It’s important to have software that monitors heat, or an alert employee who has enough experience to sense when an aggregate head is being overworked. If the budget allows, a shop should consider heads that are cooled by oil baths. However, some of those are quite bulky and heavy, and may not be suitable for smaller CNCs. Everything’s a trade-off, but bigger heads may offer the option to control speed and torque, which is handy if the aggregate is being asked to cut rather than shape.
One of the basic aggregate heads is a simple angle head that changes the direction of the tool in the spindle by ninety degrees. Basically, it points to the side instead of straight down. Benz Tooling (benztooling.com) offers several reasons for adding an angle head to a 3-axis machine, including the obvious fact that it can reduce machining time and production costs. But beyond that, the company says that angle heads enable the complete machining of complex workpieces on a machine. The point here is that a part can be fixtured once and then the head can work on it from many angles without having to resort to repeated repositioning and clamping changes. That reduces overall machining time and labor costs, but it also increases accuracy because the element of human error is removed. The part is always exactly where it was, and the machining isn’t off a smidge because it had to be reprogrammed in a new position.
Benz also points out that locations on workpieces that are difficult to access or were previously inaccessible can often be machined with angle heads. That versatility can help a shop avoid having the CNC work through most of a project and then having the woodworker resort to traditional machines or even hand-held power tools to complete some details. So often a shop needs to just drill one more hole for hardware or mill a simple tenon or pocket on the side or underside of a part, and there’s just no way to physically reach it using the vertical orientation of a standard spindle. Elaborate and complicated machining procedures can be simplified considerably by using angle heads.
Benz angle heads are designed for use in all common machining centers that have either automatic or manual tool changers. The company’s technicians can perfectly match an aggregate to a woodshop’s individual requirements.
The parts of an angle/aggregate head begin with a drive cone, which is the interface between the head and the CNC. That is attached to a locking disc which in turn works with the lock and the torque support to prevent the entire aggregate body from spinning. Below that, at the top of the actual angle head, is a scale ring that lets the woodworker manually change and lock in a fixed angle with set screws, if that’s what’s needed.
Most heads have a horizontal scale ring, while some have a vertical one and a few have both. Again, the scale ring lets the operator lock in an angle. If it’s horizontal (wrapping around the vertical part of the L-shaped angle head’s body), it controls how the head swivels in the CNC’s main spindle. If it’s vertical (where it rotates around the horizontal or lower part of the L-shaped body), it controls how the tool swivels in the smaller aggregate head’s spindle.
There are numerous types and sizes of angle head bodies available (the Benz catalog lists more than 30), and they can be used for sawing, routing, drilling, etc. at a multitude of angles. At the bottom of each is the sideways-facing output spindle that is ready to hold a tool in a clamping system and go to work. Some heads have up to four spindles, so they essentially act as mini tool changers. They just need to rotate 90 degrees (or 180) to present a new tool to the wood.
Peak Toolworks (peaktoolworks.com), the parent company of GLADU and NAP, carries a comprehensive offering of aggregate heads along with mounting parts for spindles including sleeves, spacers, cone collets and collars.
GDP Industrial Tooling (gdptooling.com) offers CNC aggregate heads, tool clamping systems, all kinds of tooling and an innovative CNC sanding head in its online catalog. The aggregate heads are made in Germany by Atemag, and they fit most CNC machining centers including Weeke, HolzHer, Homag, Onsrud, Felder, Biesse, Busellato, SCM and others, as well as point to point machines. Atemag (atemag.de) plants one tree for every aggregate sold.
Upgrading a spindle
Depending on the CNC router the shop owns, there may be a way to increase the horsepower of the spindle, improve the toolholder to a wrench-free routine, and maybe even add an automatic tool-changer. A good example is the AXYZ 4010 Twin Z machine that initially comes with a 5-hp Elte spindle. The company (axyz.com) notes that this is “a versatile, cost-effective options and very popular with first time buyers.” However, as the customer base grows and the shop begins to offer more casework options, smaller shops often find the need to upgrade the CNC just to keep up with demand. The basic spindle comes with a manual tool change option and that can be somewhat time-consuming. A better option would be a quick-release spindle and an automatic tool changer. The company has posted a short video on YouTube showing how quick and simple upgrading this machine can be. The new HSD, quick-release spindle not only diminishes downtime but also enhances performance as it reduces the possibility of human error during changeovers in multiple routing tool jobs.
HSD USA (hsdusa.com) has developed an interesting Thermal Protection Device (THPD) that’s designed to fully protect torque motors from the risk of overtemperature problems without having to connect individual heat probes. It just requires connecting the emulated output of the THPD module. It can be used in an electrical cabinet or directly on the machine and is connected to one or two motors that use a set of three heat probes (KTY84-130 or PT1000), to ensure the thermal protection of the motor itself. The device output has a variable repeated resistor used for the thermal protection of the motors.
HSD also offers a range WiFi connected spindles (ES950/ES951 e-core) where the functions include vibration and motor temperature monitoring, along with bearings temperature monitoring. The company offers a wide range of spindles and aggregate heads.
Feeling pressure?
Many spindle problems start out as collet issues. There’s a small degree of uncertainty every time one chucks a bit into a collet. For one fleeting second, there’s an image of a tool working loose halfway through the job. Our natural reaction is to bear down harder on those wrenches, and sometimes even reach for a cheater bar.
An article on the Techniks USA website (techniksusa.com) suggests that may be exactly what not to do. It explores the problem of overtightening ER collets and points out the challenge involved in providing just the right amount of torque. Trusting a collet, or indeed an entire spindle, can be hard for woodworkers who have spent years working with manual routers where a couple of wrenches and some muscles are all that’s required. Anyone who has ever had a bit work loose and destroy a part, or worse still cause an injury, is naturally going to think that the greater the pressure, the better a collet will hold. That’s not true, according to the technicians at Techniks. They note that too much torque can create a host of issues such as cracked collet pockets in the holders, cracked collets, and inconsistent run-out.
The answer, they say, is to use a torque wrench, which standardizes the amount of force being applied. That way, weak hands won’t under-tighten, and strong hands won’t overdo. Repeatability is the secret here. Another suggestion from Techniks is to switch out the standard nut for a powder-coated one. The issue is that there is friction in threads and the male and female tend to grab each other rather than slide smoothly together when they are being tightened. Powder-coated nuts apparently negate that and allow the two parts of the collet to snug up nicely and avoid any run-out. When a woodworker taps a regular collet to seat it (and we’ve all done that), what they are doing is releasing some of the friction and allowing the threads to mesh a little better. But once the machine starts up, Techniks says that “the tool shank will find its point of lowest energy and will, once again, move out of tolerance”. Powder-coated collet nuts apparently alleviate this radial distortion and allow the collet to grip the tool tightly before it begins to rotate.
It’s an interesting article, and it provides a convenient introduction to Techniks’ P3 ER collet system. The P3 (also known as the Parlec Pro Precision) has a special anti-friction coating on its 30-degree collet face. This enhances the ability of the powder-coated collet nuts to reduce friction buildup. P3 ER collets also have a reduced number of slots, making the collets more rigid, which of course means less radial distortion.
Mid America Woodworking Machinery (cnc-tool.com) notes that neglecting collet maintenance can result in “a dramatic drop in performance, which reduces productivity and increases costs due to higher scrap rates and potential machine downtime.” The company lists tool slippage, tool run out and scoring of both the holder and the tool shank among those issues. A lack of collet maintenance (or timely replacement) is one of the most common causes of premature tool failure. The typical life span of a collet is between 400 to 600 hours, which roughly translates to between two and three months with the collet being used eight hours a day. Mid America underscores the notion that “keeping your CNC tool holders clean is just as important as keeping your cutting tools sharp.”
To that end, CleBitCo (clebitco.com) offers spindle toolholder and collet cleaning kits for HSK, ISO and ER parts, along with Nu-Tool’s two-part holder/collet cleaner. Part 1 is a powerful cleaning solution for removing rust and debris from tool holders and collets. Part 2 is a specially formulated protectant that will deter rust and repel dust from tool holders and collets. In these days of hard-to-find replacement parts, CNC owners might want to pay special attention to maintenance on spindles, aggregate heads, and all of the other sensitive elements of a CNC routing system.
This article was originally published in the January 2022 issue.
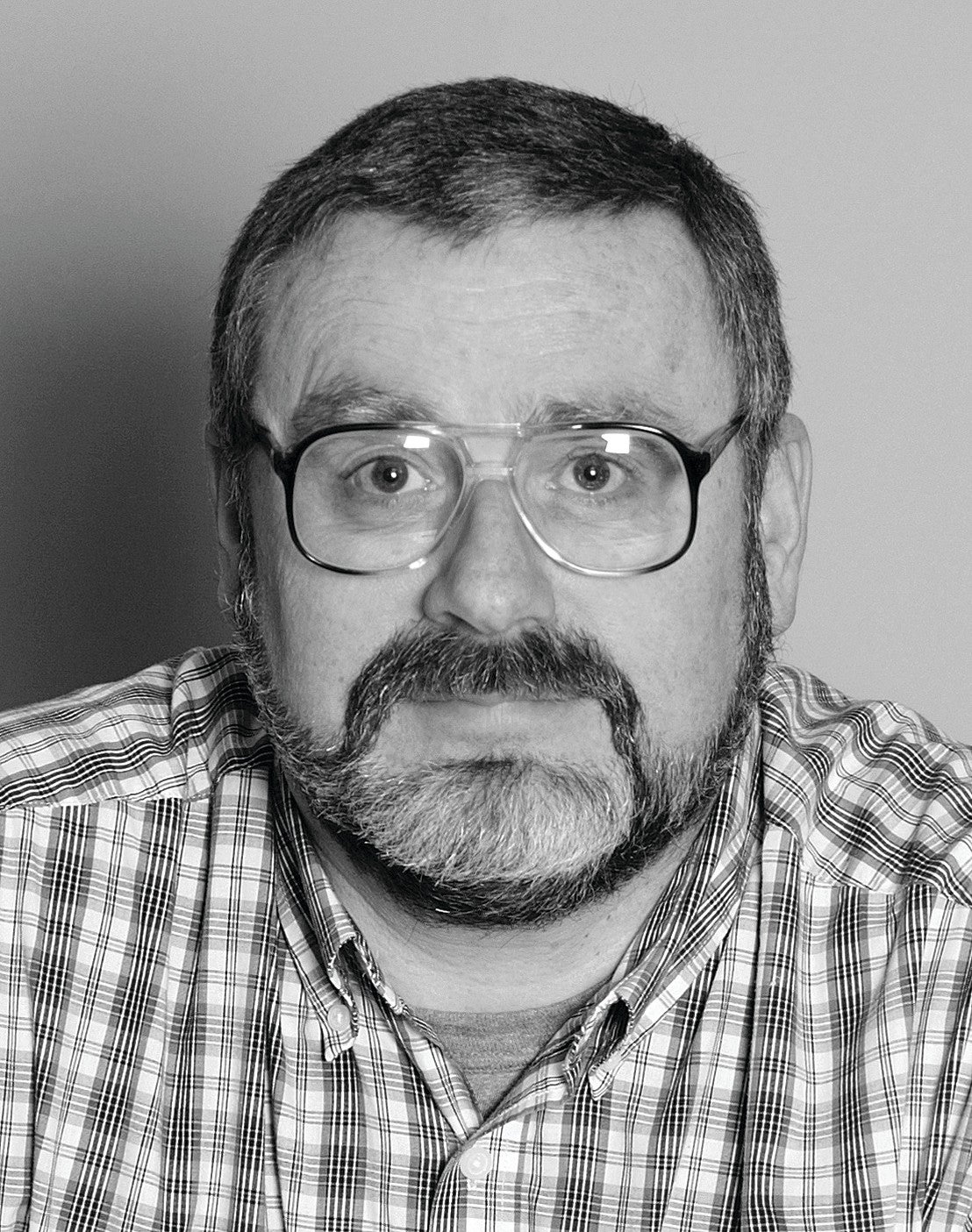