Working smarter, not harder
Make the moving experience safer and more efficient with these material handling solutions
Material handling is a wide-ranging concept that covers moving, protecting, storing, controlling, and tracking raw materials and subassemblies through the entire manufacturing and installation processes. It includes handling in the woodshop and at the jobsite, and while traveling between the two – from sheet stock arriving at the loading dock to the last drawer pull needed to complete an installation of casework or furniture.
Given those broad parameters, it makes sense to break the concept into a few separate processes to make it more manageable, and more industry specific. In the woodshop, material handling includes storage units such as shelving, bins and racks; mobility equipment such as conveyor belts, carts, dollies, pallet trucks, forklifts and delivery trucks; and placement hardware including CNC loaders/unloaders and collaborative robots (cobots). All these elements are designed to help a shop work smarter, safer, faster, and more efficiently. How they do that depends on how sophisticated the equipment is, and how efficiently it is used. And a big part of that is the speed at which evolution in this field is accelerating as robots continue to expand their role in moving materials to machines, along with feeding and harvesting parts.
Lifting solutions
Not every shop needs every available piece of equipment when it comes to managing material flow. Shop managers may want to identify bottlenecks first and apply technologies to ease those right away. For example, if sheet stock is being wheeled on manual carts from the CNC to the edgebander, maybe it’s time to install a conveyor system. That triage approach (fix the immediate problem first) can then be followed up by a systemic, shop-wide audit to discover where other handling equipment can help improve flow.
And that’s where things can get sticky, simply because the range of equipment is so wide. A good place to start exploring is a single supplier that carries many different brands. For example, a quick look in the Stiles Machinery (stilesmachinery.com) catalog reveals sections that cover jig and bridge cranes, small and large vacuum lifts, conveyors, transfer carts, sheet-turning benches and lift tables. One section of the catalog is dedicated to Schmalz’s Jumbo Ergo, which is a large vacuum lifting system that lets a single employee move, lift and place materials that weigh up to 660 lbs. It has controls that look like the handlebars on a motorcycle, and there’s even a bike-like throttle. (Yup, it’s kind of fun to use.) Working with a single supplier can help a shop create an integrated system, rather than purchasing a few unrelated pieces of equipment.
Beaver Industrial Supply (beavertools.com) is another wide-reaching supplier, and here a woodworker can find smaller manual equipment (as in, less automated) such as carts and scissor lift tables. The company carries four different JET lift tables, one of which (the SLT-1100) can raise a stack of plywood weighing up to 1,100 lbs. on its 63” x 31-1/2” table and raise it to a maximum height of 36”. That height works well for most traditional machines and CNCs. The scissors table is operated by a hydraulic foot pump and it’s on locking casters so it can be moved from a lumber rack to an infeed table. A lift table takes some of the strain out of loading and moving large materials, and contributes to smarter, safer workshop practices.
Martin Woodworking Machines (martin-usa.com) makes top quality scissors lift carts, and the company also supplies the very interesting Barth VakuuCar. This is a workbench, vacuum holding system and transportation device all rolled into one. It’s adjustable to different employees’ optimum workbench heights, holds work rock solid with three vacuum cups, and has a swinging frame that lets a single woodworker work with and move some very large panels.
Southworth Products (southworthproducts.com) also manufactures scissors lift tables, along with a wide range of other equipment that can move material through the shop and change levels between machines as it goes. Its catalog is designed around improving productivity while reducing the possibility of employee injury, including back pain. Most of the solutions can be integrated into large production environments, but they’re also just at home in one- or two-man shops.
Grizzly Industrial (grizzly.com) offers a handy pallet stacker, model T31643, that’s ideal for tight spaces.
JPW (jpwindustries.com), makers of JET and Powermatic, has a division that makes pallet trucks, utility carts and scissor lift tables. The pallet trucks can lift 5,500 to 8,000 lbs. Top of the line is the JTX-2748B. The company’s utility carts (eight models, differentiated by size) are ideal for transporting smaller materials such as hinges, slides and pulls around the woodshop.
SawTrax (sawtrax.com) may be more familiar as a manufacturer of panel saws, but the company also makes some interesting reconfigurable carts and clever dollies that allow a single employee to handle some very large materials. There’s the small footprint Panel Express that can transport full sheets of MDF, plywood, or countertop materials across rugged terrain. The Scoop Dolly is designed to handle up to half a ton of millwork (doors, windows, stair parts) and unlike standard hand trucks, it can move both forward and backward, plus side to side. Just the carrying section pivots, instead of the entire dolly, so it’s easy to use with one person. Once loaded and tilted back, the load on the Scoop Dolly remains stable without needing to be supported by the operator. The Dolly Max can carry large loads of lumber and has adjustable posts to accommodate different dimensions, and the Rack & Roll Dolly lets a woodworker sort, store and move a collection of sheet goods in full or partial sheets.
Clever ideas
Rockler (rockler.com) carries several handy items for small shops including the Gorilla Gripper plywood carrier and the Material Mate panel cart. The Gripper clamps onto the top edge of a sheet so the employee doesn’t need to bend or stoop, and once hoisted most sheet sizes can be carried around the shop with one hand comfortably locked in place over one shoulder. The cart has a flip-top that lets an employee load a sheet from a vertical stack and then flip it horizontally to feed into a machine such as a table saw. The cart can be locked so the top is flat, and the company offers some options for adding a worktop and turning it into a temporary workbench when it’s not handling sheet stock.
That duality of purpose is a space-saving way to handle materials, and the same philosophy is evident in JLT’s Buddy system. The James L. Taylor Mfg. Co. (www.jamesltaylor.com) has developed an application where one side of a machine is used to edge-glue solid wood panels, while the other side is used to glue those panels into cabinet door frames. It’s a smart, safe way to handle material while also saving time and money.
For larger shops, some manufacturers may be able to offer handling equipment that uses the same control or audit software as the machines that it serves. With all the apps being developed to track machine performance and maintenance, it’s a good idea to ask if the ancillary material handling equipment can be monitored in the app, too.
Choice Machinery Group (choicemachinerygroup.com) makes the 9265, a pivoting vacuum hoist with a rotating arm. It handles panels up to 5’ x 12’, and 400 lbs. The height (lift) range is 4” to 60” and it can rotate stock up to 180 degrees and pivot to 360 degrees. This is a single-phase, household current machine drawing 15 amps at 120 volts. The caster-mounted machine lets a woodworker easily pick up, flip over, and spin countertop and panel materials.
SCM Group’s material handling solutions include Mahros stackers, conveyors, carriers and flippers, so a shop might be able to equip itself with a single brand. If not, SCM (scmgroup.com) also carries the Flexstore ELR, which is a 3-axis panel mover that manages both homogenous and mixed stacks (different dimensions, veneer or colors) for nesting and sizing cells. It’s a strong machine with gentle fingers that can move sheet stock quickly and efficiently without harming surfaces.
Woodshops that are working with solid wood can reduce handling time dramatically by adding a TigerStop (tigerstop.com) to the miter saw station. This device can push, pull and position material up to 180 lbs., and turn an existing manual machine into a fully automatic, lean manufacturing asset. And the same company also offers SawGear, which is a simpler but still very intuitive automated stop (not designed to push feed) that also attaches to an existing saw or drill press. It lets a woodworker do away with the measure twice, cut once concept, and in fact can eliminate tape measures, manual stop blocks, and clamps from the manufacturing process.
In a similar vein, Atlantic Machinery (atlanticmach.com) offers the OMGA Stop, a numerically-controlled positioning system with 6, 10, 13, 16 or 22 feet of useable traverse (available in left or right configurations). It can be used in conjunction with a variety of machines such as up-cut, radial arm, table and miter saws and it eliminates the need for manual measuring.
For the spray booth
Handling parts in a paint booth presents two big problems – space and mobility. Doors, drawer fronts, shelves and panels are large in at least two dimensions. So, running a full kitchen through a booth requires careful planning and even more careful moving of wet parts. There have been a couple of significant improvements in this area over the past couple of years. Drying racks from Paintline (thepaintline.com) let a woodworker spray, dry and move parts through the booth without marring. And the Pivot Line from Guffey Systems (guffeysystems.com) combines rails and hangers for non-contact finishing and handling. A shop can go from bare wood to final coat without having to touch the finished surface of any components.
This article was originally published in the January 2022 issue.
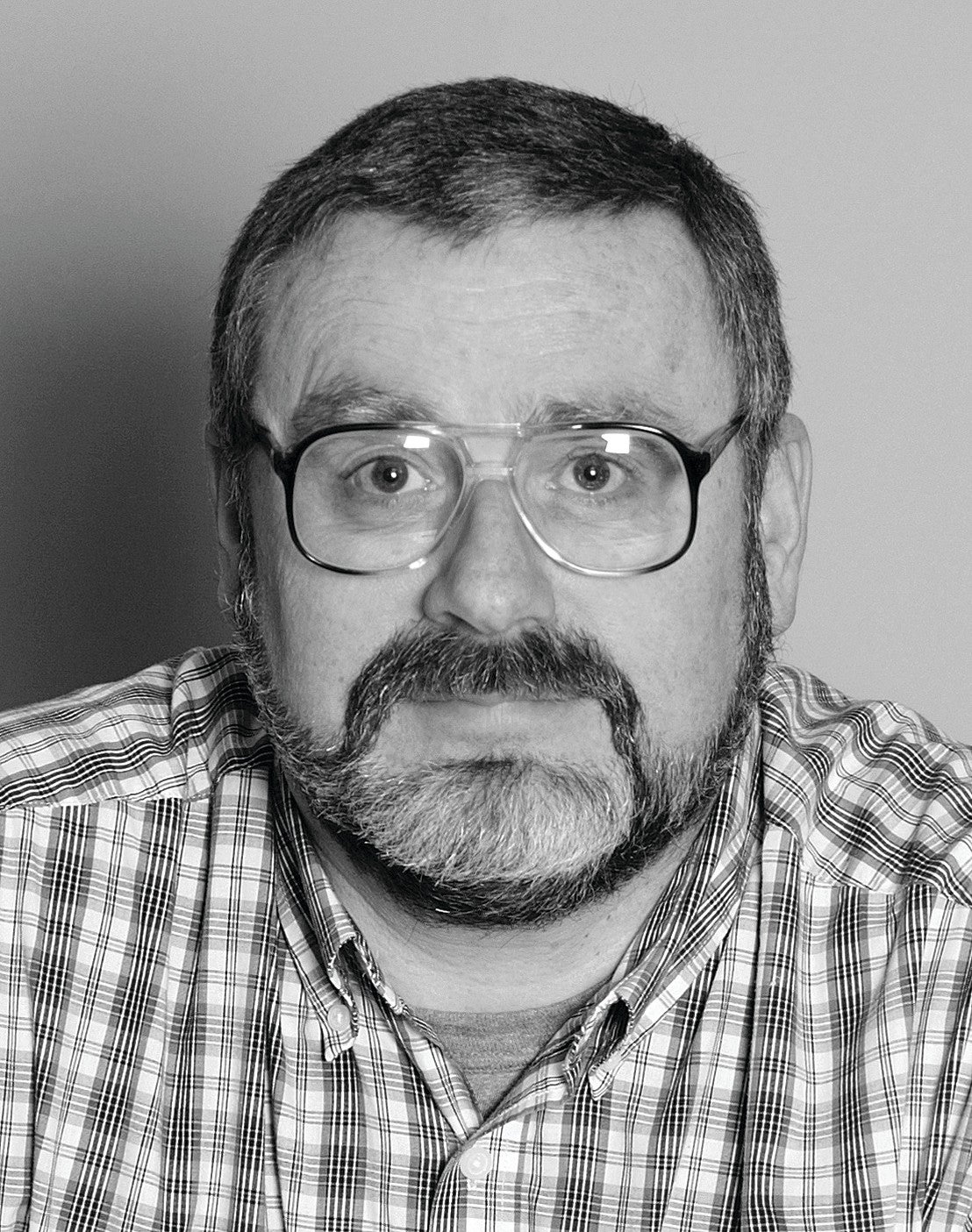